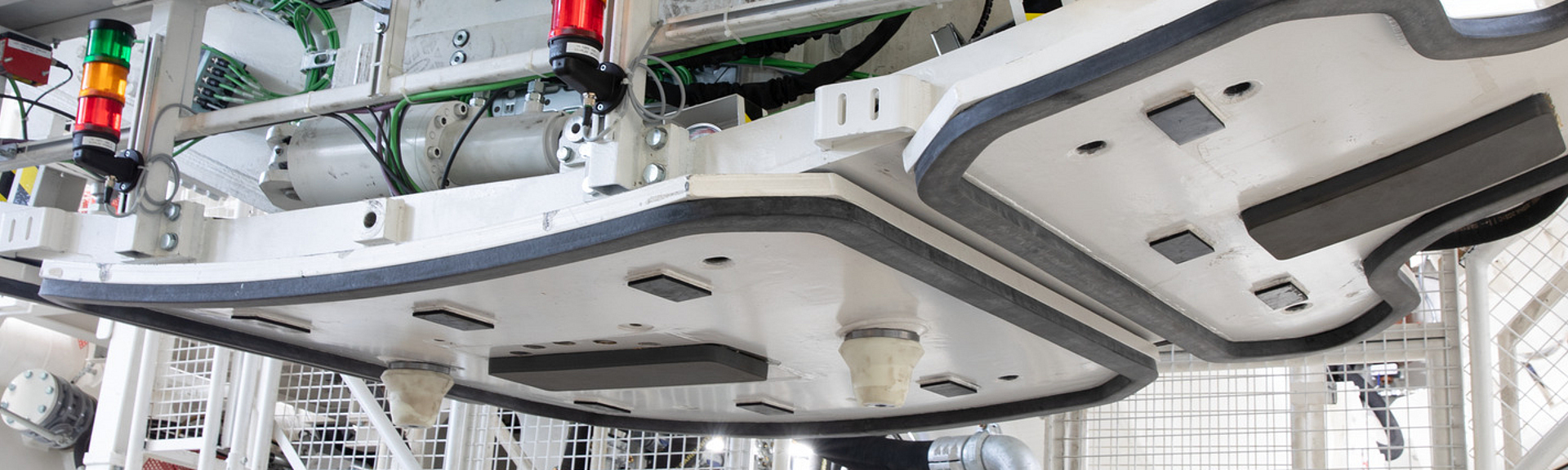
Tunnelbau
Leistungs- und Effizienzsteigerung von Tunnelbohrmaschinen
Die Entwicklung der Tunnelbohrmaschinen (TBM) für Locker- wie Hartgestein war in den letzten Jahrzehnten geprägt von höheren Drücken, größeren Durchmessern und Multimode-Funktionalität. Neben dem Trend zur Digitalisierung sind aufgrund des Fachkräftemangels und des Wunsches nach mehr Qualität und Systemleistung Automatisierung, bedienerunterstützende oder autonome Systeme zu wichtigen Entwicklungszielen geworden. Neben diesen Aspekten wird das permanente Ziel einer verbesserten Arbeitssicherheit und die anstehende Überarbeitung der europäischen TBM-Sicherheitsnormen die TBM-Technologie zusätzlich stark in Richtung Automatisierung und ferngesteuerten Betrieb lenken. Der Beitrag stellt den aktuellen Stand der Technik vor dem Hintergrund dieser besonderen Bedingungen dar.
Treiber der TBM-Entwicklung
In den vergangenen Jahrzehnten waren die Entwicklungsziele im maschinellen Tunnelbau geprägt durch schwierigere Bodenverhältnisse, höhere Stützdrücke, größere Durchmesser und Tunnellängen sowie Leistungs- und Effizienzsteigerungen. Zu diesen Trends, die weiter wirksam bleiben, rücken Nachhaltigkeit und Personalmangel neben dem fortwährenden Ziel höherer Arbeitssicherheit in den Fokus. Intelligente Datenmanagementsysteme, Künstliche Intelligenz und Automatisierung führen zu einem neuen Ansatz für den industrialisierten, mechanisierten Untertagebau, der weitere Schritte zu mehr Sicherheit, Qualität und Wirtschaftlichkeit ermöglicht.
Automatisierung
Als industrieller Prozess bietet der maschinelle Tunnelvortrieb grundsätzlich gute Voraussetzungen zur Automatisierung. Für die Arbeitsabläufe im Bereich der TBM sind derzeit zwei Tendenzen zu beobachten: bedienerunterstützende Systeme und vollautomatische Teilsysteme.
Bedienerunterstützende Teilsysteme
Bedienerunterstützende Systeme zielen darauf ab, wiederkehrende Arbeitsabläufe zu teilautomatisieren. Damit wird zum einen der Bedienende entlastet, zum anderen bietet sich die Chance, Fehlbedienungen zu vermeiden und eine Interpretationshilfe für den jeweiligen Betriebszustand des Teilsystems zu integrieren. Aktuelle Beispiele sind etwa die Steuerung der Vortriebsmaschine mit Darstellung des Druckschwerpunkts der Vortriebszylinder als Center of Trust (CoT) und Nutzung desselben als Steuergröße oder die bedarfsgerechte Befüllung der Dichtkammern der Schildschwanzdichtung (Adaptive Tailskin Sealing System). In dem Zusammenhang sind ebenfalls die vielen heute von den Betreibern als selbstverständlich angesehenen Abfragen, Verriegelungen und Warnhinweise in den SPS-Programmen der TBM-Steuerung zu nennen.
Vollautomatische Teilsysteme
Neben dem Tübbing-Einbau sind die Lieferung von Tübbings und Verbrauchsmaterialien, der Abtransport des Ausbruchsmaterials und die Wartung der Geräte wiederkehrende Tätigkeiten im TBM-Vortrieb.
Tübbing-Handling
Der am häufigsten wiederkehrende Vorgang im maschinellen Schildvortrieb ist der Tübbing-Transport und -Einbau. Daher ist der Ansatz zur Automatisierung dieser Prozessschritte sowohl aus wirtschaftlichen wie aus Sicherheitsgründen in den Fokus gerückt. Insbesondere bei langen Tunneln mit entsprechend vielen Tübbings kann sich eine Investition in vollautomatische oder bedienerunterstützende Systeme lohnen. Vollautomatische Teilsysteme können alle Vorgänge des Tübbing-Handlings vom Entladen des Transportfahrzeugs bis zum Aufnehmen des Tübbings durch den Erektor und den Ringbau selbst umfassen umfassen (Abb. 1). Für die Einführung automatisierter Umschlagsysteme müssen die Tübbings, die Ladekonfiguration und der Tübbing-Stapel auf dem Lieferfahrzeug für die Automatisierung geeignet sein. Während es sich bei den Tübbings um hochpräzise Bauteile handelt, die bereits mit Hilfsmitteln zur automatischen Identifizierung ausgestattet sein können, erhöhen sich durch die Automatisierung die Anforderungen an die geometrische Genauigkeit der Stapel, der Stapelhölzer und der Stapelposition auf dem Versorgungsfahrzeug. Das Greifsystem für die Tübbing-Aufnahme durch einen Übergabekran oder Erektor kann kein manuelles Einschrauben von Tübbing-Spindeln mehr beinhalten und wird daher durch Vakuumheber oder andere Greifvorrichtungen realisiert.
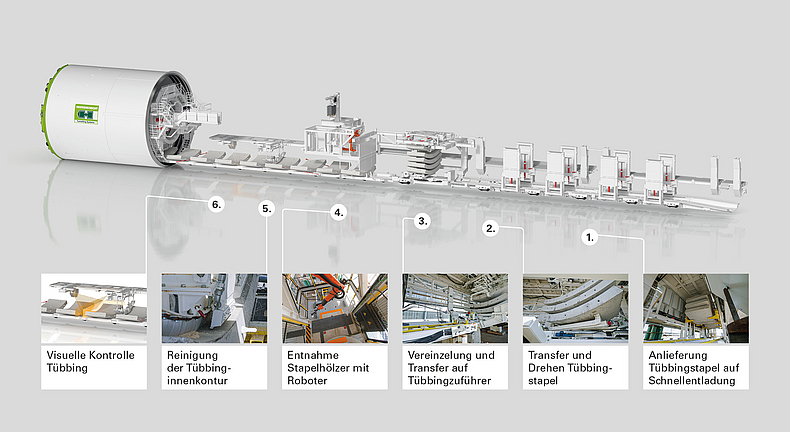
Automatisierter Tübbing-Umschlag im Nachläufer
Unabhängig vom Tübbing-Handling vor dem Tunnelportal ist auf der TBM eine Sichtkontrolle der einzelnen Tübbings beim Entladen und vor der Übergabe an den Erektor sinnvoll. Die visuelle Kontrolle und eventuelle Einleitung von Korrekturmaßnahmen umfassen die Erkennung von Transportschäden, die korrekte Position der Tübbing-Dichtungen und anderer Einbauten oder die Verunreinigung der Oberfläche durch Schmutz oder Eis bzw. Schnee, die zu einer Fehlfunktion der Vakuumaufnahme führen können. Um eine Störung des Ringbaus zu vermeiden, bei dem der Erektor-Fahrer Probleme erst zum Zeitpunkt des Ringbaus erkennt, sollte ein automatisierter Tübbing-Umschlag auch automatische Inspektionssysteme durch Kameras umfassen. Dabei kann die Bildanalyse mittels Künstlicher Intelligenz unterstützen. Eine präventive Reinigung der Tübbing-Innenkontur ist ebenfalls ratsam. Je nach Tübbing-Design und den Vorbereitungsprozessen kann ein automatisierter Tübbing-Umschlag auch eine automatische Dübelmontage umfassen. Auch bei einem vollautomatischen System muss die Möglichkeit bestehen, die Tübbings sicher von Hand zu transportieren. Dazu gehört die Möglichkeit, sie von ihrer Einbauposition im Schildschwanz zurück auf das Transportfahrzeug und schließlich aus dem Tunnel zu bringen. Mehrere 10-m-TBM mit automatisiertem Tübbing-Handling im Nachläufer wurden im vergangenen Jahr ausgeliefert und in Betrieb genommen.
Ringbauunterstützung
Für den Ringbauprozess können Sensortechnologien zusätzliche Informationen für den Ringbau generieren, die auf dem mobilen Erektor-Tableau angezeigt werden, wie z. B. die Ringbauluft oder die relative Position des Segments zu seinen Nachbarsegmenten (Abb. 2). Mit der Bereitstellung solcher Daten für den Erektor-Fahrer müssen keine manuellen Messungen von den Plattformen des Erektors mehr durchgeführt werden. Auf diese Weise können Sicherheitsrisiken beseitigt und die Anzahl der Mitarbeiter für den Ringbau reduziert werden.
Automatischer Ringbau
Der nächste Schritt, der über die Bereitstellung von Informationen hinausgeht, ist der vollautomatische Ringbau, bei dem kein Personal im Ringbaubereich anwesend ist. Der Ringbau beinhaltet die Handhabung schwerer Betonfertigteile in einem Bereich, der insbesondere bei kleinen TBM als beengter Arbeitsraum angesehen werden kann. Schwieriger Zugang und eingeschränkte Sicht sind typische Herausforderungen. Daher sind Sicherheitsaspekte neben Qualität und Wirtschaftlichkeit die wichtigsten Argumente für den automatisierten Ringbau. Die Hauptkomponente des zu automatisierenden Ringbausystems ist der Erektor. Wie bei allen Automatisierungsprozessen muss die genaue Position aller beteiligten Komponenten bekannt sein. Alle beweglichen Teile des Erektors, die Vortriebszylinder und der Tübbing-Zuführer sind deshalb mit Positionsmesssystemen auszurüsten. Für einen automatisierten Ringbauprozess ist nicht nur die exakte Position aller Erektor-Funktionen und anderer beweglicher Teile, sondern auch die exakte Position und Ausrichtung der Segmente auf dem Tübbing- Zuführer erforderlich. Bei Verwendung von optischen Sensoren ist eine ungehinderte Sicht der Sensoren unerlässlich, weshalb z.B. bei Reinigungs- und Wartungsarbeiten an den Verpressleitungen im Schildschwanz eine unnötige Verschmutzung der Sensoren zu vermeiden ist.
Testserie in Schwanau
Bei Herrenknecht in Schwanau wurden automatische Ringmontagesysteme für eine 3-m- und eine 8-m-TBM entwickelt und mit Versuchsanordnungen in realer Größe getestet (Abb.3).
Sobald automatisierte Systeme installiert werden, müssen physische Barrieren mit verriegelten Zugangstüren installiert werden, um den Zugang zu dem Bereich mit automatisierten Bewegungsund/ oder Handhabungsvorgängen auszuschließen. Folglich sind solche Bereiche innerhalb des Nachläufers oder des Ringbaubereichs nur während des manuellen Betriebs oder zu Wartungszwecken zugänglich. Automatisierte Systeme haben somit Auswirkungen auf das Arbeitsumfeld und die Arbeitsabläufe. Automatisierte Systeme werden mehr Sensorik und computergesteuerte Kontrollsysteme erfordern. Insbesondere die rauen Umgebungsbedingungen in einem Tunnelvortrieb müssen bei der Auswahl und Auslegung der Komponenten berücksichtigt werden. Ebenso muss das Wartungspersonal vor Ort entsprechend qualifiziert werden.
Semikontinuierlicher Vortrieb
Neben der Automatisierung der Teilprozesse lohnt sich für die Leistungs- und Effizienzsteigerung der Blick auf den Gesamtprozess des Schildvortriebs mit der wiederkehrenden Abfolge von Vortrieb und Ringbau. Wenn es gelingt, die Vortriebsmaschine so zu gestalten, dass während des Vortriebs der Einbau der Tübbings erfolgen kann, ohne dass die TBM angehalten werden muss und dennoch eine Richtungssteuerung entlang des Trassenverlaufs gelingt, kann die Vortriebsleistung gerade bei langen Vortrieben merklich gesteigert werden. Dabei steht die Zeitspanne des Ringbaus nun ebenfalls für den Vortrieb zur Verfügung. Mit diesem Ansatz werden Vortriebe mit eher geringerer Vortriebsgeschwindigkeit deutlich beschleunigt, da aufgrund der erforderlichen Gesamtdauer für den Vortrieb ausreichend Zeit für den Ringbau zur Verfügung steht, sobald die Vortriebspressen so weit ausgefahren sind, dass das Einbaumaß im Schildschwanz den Tübbing-Einbau zulässt . Auf Seiten der Maschinentechnik bedingt dies Vortriebszylinder mit mehr Hub und einen entsprechend längeren Mittelschuss und Schildschwanz sowie erhöhte Anforderungen an Sensorik und Hydraulik. Beim Konzept des bereits ausgeführten semikontinuierlichen Vortriebs stoppt die Vortriebsmaschine mit Erreichen des erforderlichen Pressenhubs zunächst für den Einbau der ersten beiden Tübbings, ehe die weiteren Tübbings und der Schlussstein während des verbleibenden Vortriebs versetzt werden. Die Tübbings erfahren aufgrund des Einbaus während des Vortriebs eine höhere Belastung, die beim Design hinsichtlich der Spaltzugbewehrung und der Nachweise zu berücksichtigen sind. Ebenso sollte die gesamte Logistikkette des Vortriebs entsprechend der höheren Leistung und des Wegfalls der klassischen Ringbauphase mit stillstehender Vortriebsmaschine geplant werden. Diese Ringbauphase entfällt als zumindest teilweise mögliche (Puffer)zeit für die Versorgungsfahrzeuge oder für einfache schnelle Wartungsarbeiten.
Mehrere 10-Meter-TBM wurden nach dem Ersteinsatz für den Chiltern-Tunnel (UK) mit dem System ausgerüstet und werden 2023 als weitere Anwendung in Betrieb genommen.
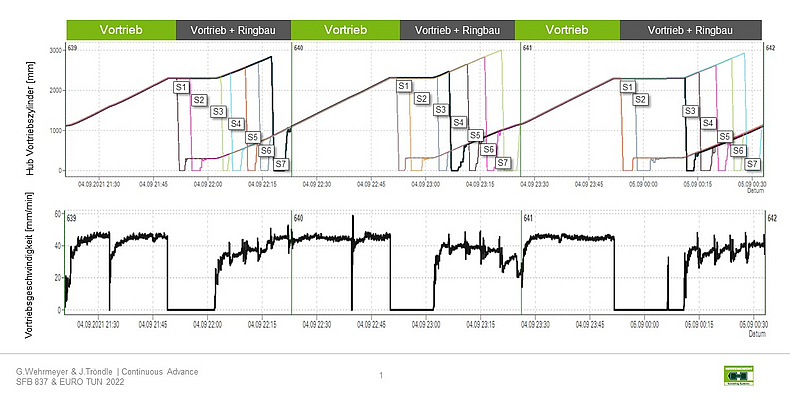
Realisierung des semikontinuierlichen Vortriebs im Ersteinsatz beim Vortrieb der Schildmaschinen für den Chiltern-Tunnel
Separationsanlagen
Separationsanlagen kommen als nachgeschaltete Trenneinrichtung für den Bodenaushub bei Mixschilden und Variable-Density-TBM zum Einsatz. Um auch hier die Automatisierung und Digitalisierung voranzutreiben, ist es unumgänglich, die Separationstechnik schrittweise weiterzuentwickeln.
Eine dieser Innovationen ist das Density Regulation System (DRS), das im Bypass zum Kreislauf der Primärseparation mit Siebmaschinen und Hydrozyklonstufen installiert wird, um zusätzlich die Dichte der Feinsttrennung der Sekundärseparation zu regulieren. Die dabei eingesetzte dritte Zyklonstufe zeichnet sich durch einen noch kleineren Trennschnitt aus, der die Standzeit der Suspension erheblich erhöht. Durch den Eindickungseffekt des Unterlaufs und des Austrags für die Feinsttrennung mit Zentrifugen oder Filterpressen wird weiter deren Effizienz durch die Reduzierung des Wassergehalts der ausgetragenen Feststoffe erheblich verbessert und die Prozesskapazität in Tonnen pro Stunde erhöht, was die Investitionskosten senkt.
Weiter wurde das sogenannte Noise and Vibration Cancelling System (NVCS) zur akustischen Optimierung der Anlage entwickelt, um die Auswirkungen auf die Umgebung der Baustelle zu reduzieren. Es reduziert durch Phasenverschiebung mittels Software effektiv Lärm und Vibrationen, die von den Siebmaschinen erzeugt werden. Die Beeinträchtigung von Anwohnern wird ebenso minimiert wie die allgemeinen Arbeitsbedingungen für das Personal verbessert. Die effiziente Einbindung der Separationsanlagen mit ihren Betriebsdaten in das Datenerfassungs- und -managementsystem der TBM ermöglicht die Visualisierung und Analyse aller relevanten Prozessparameter und ist die Basis für die weitere Automatisierung der Anlagen.
Datenmanagement
Während des TBM-Betriebs laufen viele Prozesse gleichzeitig ab. Jeder Teilprozess wird durch Sensoren überwacht und durch Aktoren gesteuert. Alle Prozessgrößen und Steuerungsvorgänge sowie Parameter und Störmeldungen werden über die gesamte Projektdauer in einem Datenmanagementsystem aufgezeichnet. Bei durchschnittlich 2.000 Sensoren, einer Datenaufzeichnungsrate von einer Sekunde und einer Projektlaufzeit von zwei Jahren müssen deutlich mehr als 100 Mrd. Datenpunkte erfasst und gespeichert werden. Beim Einsatz mehrerer oder komplexerer Maschinen und längeren Projektlaufzeiten kann sich diese Zahl schnell verdoppeln. Die Menge der TBM-Vortriebsdaten wird durch Daten aus der Peripherie, der geotechnischen Instrumentierung und anderen baubetrieblichen Prozessen weiter vergrößert.
Ferner muss das Datenmanagement sowohl mit strukturierten als auch mit unstrukturierten Daten umgehen. Strukturierte Daten umfassen Zeitreihen, Metadaten für Sensoren oder aggregierte Werte für einzelne Prozesse, während Bilder, Berichte oder geotechnische Daten als unstrukturierte Daten bezeichnet werden. Ein geeignetes Datenmanagementsystem ist in der Lage, die unterschiedlichen Datentypen und -formate zu verarbeiten, miteinander zu verknüpfen und Beziehungen und Bezüge herzustellen. Derart verarbeitete Daten stellen einen enormen Wert für bedienerunterstützende Systeme und zur Leistungsoptimierung des Vortriebs, der Dokumentation und für zukünftige Anwendungen und Entwicklungen dar.
Der Newsletter der BG BAU
Hier erhalten Sie alle wichtigen Meldungen und aktuelle Informationen zum Thema Arbeitsschutz per E-Mail – so etwa auch Hinweise zu neuen Arbeitsschutzprämien und Seminarangeboten.
Sie möchten keine Ausgabe der BauPortal verpassen? Klicken Sie einfach das entsprechende Kästchen in den Profileinstellungen an. Den Link zum Profil finden Sie am Ende jedes Newsletters oder direkt nach der Anmeldung.
Ein weiterer Aspekt der Betriebsdatenverarbeitung bezieht sich auf die TBM-Wartung. Eine Wartungssoftware kann die Daten überwachen, mögliche Fehlfunktionen frühzeitig erkennen und notwendige Schritte einleiten, bevor ein ungeplantes Ereignis eintritt. Durch automatisierte Auswertungen, z. B. der Betriebsstunden von Komponenten, werden notwendige Wartungsaufgaben frühzeitig erkannt und dem Betreiber gemeldet. Dies schafft Planungssicherheit, da die notwendigen Komponenten rechtzeitig bestellt und die Arbeiten entsprechend eingeplant werden können.
Ein konkreter Anwendungsfall für einen Predictive Service ist z. B. die Zustandsüberwachung der Abbauwerkzeuge, kombiniert mit einer Werkzeugwechselprognose in Verbindung mit den real vorhandenen Bodenverhältnissen. Ziel ist es, auf Basis der aktuellen und vergangenen Vortriebsbedingungen eine frühzeitige Prognose für notwendige Werkzeugwechsel zu erstellen und diese dynamisch mit der Vortriebslänge anzupassen.
Der Wiedereinsatz aufbereiteter TBM-Baugruppen und -komponenten oder ganzer TBM hat einen großen Einfluss auf die Verringerung des CO2-Fußabdrucks der Ausrüstung. Die Verfügbarkeit der Betriebsdaten und der Wartungshistorie einer TBM oder ihrer Unterbaugruppen ist eine Schlüsselinformation, um die verbleibende Lebensdauer und/oder die erforderlichen Schritte der Wiederaufarbeitung zu bewerten. In Bezug auf Nachhaltigkeit und Kreislaufwirtschaft kann für das nächste Projekt ein qualitativ hochwertiges und zuverlässiges Produkt erstellt werden.
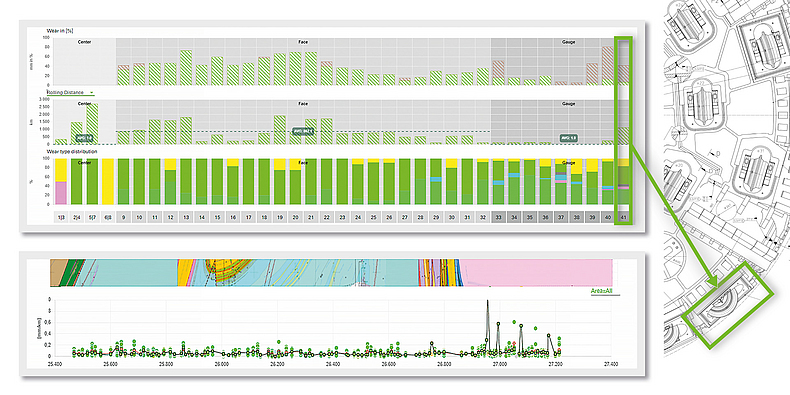
Schneidrollenlebenszyklus der Herrenknecht Tools.on Software
Schlussfolgerung
Automatisierung und intelligentes Datenmanagement haben Einzug in den maschinellen Tunnelbau gehalten und werden das Arbeitsumfeld unter Tage weiter verändern und die Tendenz zu nachhaltigeren Lösungen unterstützen. Die ersten automatisierten Systeme sind im Einsatz. Mit den Baustellenerfahrungen dieser Systeme und den daraus resultierenden weiteren Entwicklungsschritten werden weitere Verbesserungen in Richtung eines sicheren und effizienteren Betriebs und nicht zuletzt attraktiver Arbeitsplätze erzielt werden.
Autor
Ausgabe
BauPortal 2|2024
Das könnte Sie auch interessieren
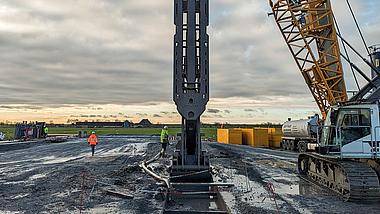
Tunnelbau
ElbX: das Tunnelbauwerk für die Energiewende
Die Elbquerung ist einer der herausforderndsten Projektabschnitte bei der Errichtung der Stromtrasse SuedLink. Ihr Bau startete mit anspruchsvollen Spezialtiefbauarbeiten.
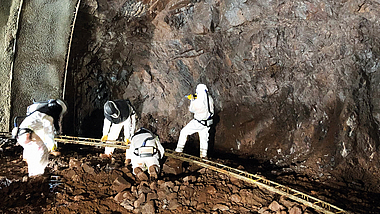
Tunnelbau
Konzepte und Schutzmaßnahmen bei Vortriebsarbeiten am Brandbergtunnel
Im Brandbergtunnel im Elztal wurde im März 2020 wurde ein umfangreiches Schutzkonzept für Vortriebsarbeiten in asbesthaltigem Gestein erarbeitet und anhand gewonnener Erkenntnisse laufend fortgeschrieben.
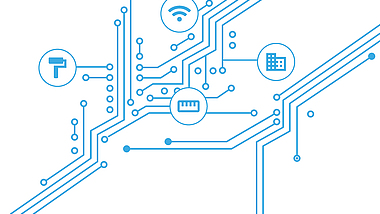
Tunnelbau, Digitalisierung
Start-up-Lösung von „hyperTunnel“
Das britische Start-up „hyperTunnel“ möchte mit digitalen Zwillingen und Robotern die Gefährdungen beim Tunnelbau erheblich reduzieren. Keine Beschäftigten sollen die Baustelle betreten müssen.