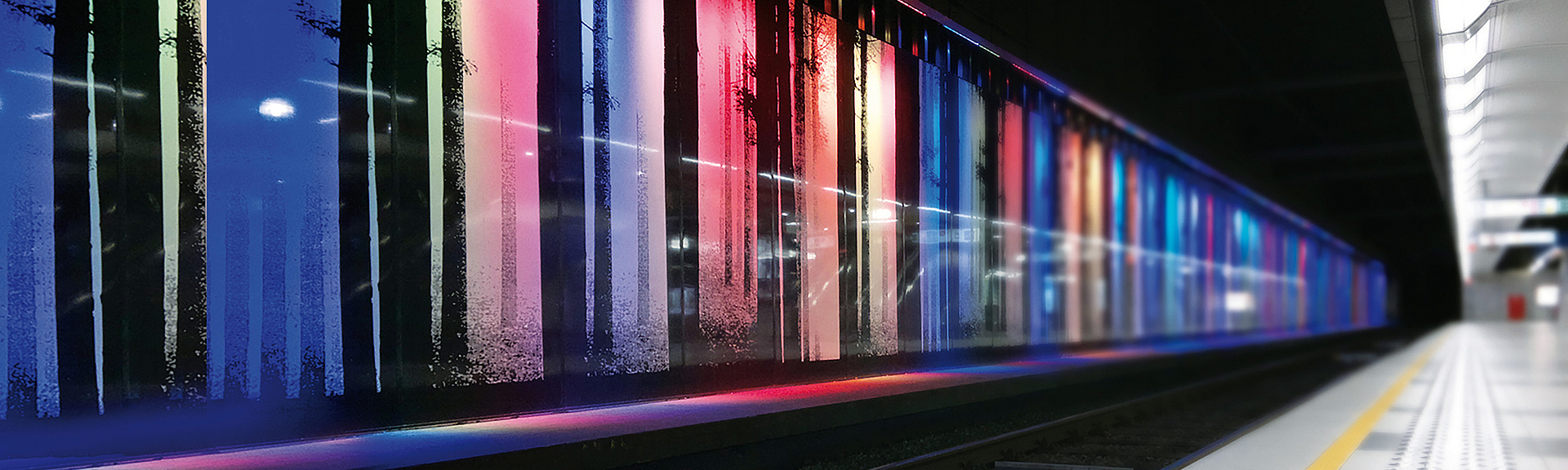
Abdichtungstechnik/Bautenschutz
Wandbekleidungen in Tunneln
Wandbekleidungen im Tunnel sind meist besonderen Anforderungen ausgesetzt: Resistenz gegen permanente Feuchtigkeit und Nässe, teilweise hochkorrosive Atmosphäre sowie extreme Druckunterschiede durch vorbeifahrende Fahrzeuge mit dynamischen Belastungen sollen kombiniert werden mit Brand- und Schallschutzanforderungen, einfacher Reinigung und Instandhaltung sowie wiederholter Demontierbarkeit bei gleichzeitig hohen optischen Anforderungen.
Einbauten in Straßen- und Bahntunneln, wie z. B. Wandbekleidungen oder Befestigungslösungen, sind oft Belastungen durch Korrosion und durch Druckschwankungen, die durch den Lastwechsel der passierenden Fahrzeuge (Winddruck und -sog) hervorgerufen werden, ausgesetzt. Um Funktionsbeeinträchtigungen zu verhindern, sind Lösungen gefragt, die widerstandsfähig gegen Korrosion und dynamische Lasten sind und darüber hinaus auch noch weitere Anforderungen erfüllen, die in Tunneln wichtig sind. Dazu zählen z. B. Brand- und Schallschutz, aber auch eine einfache Wartung bestehender Systeme.
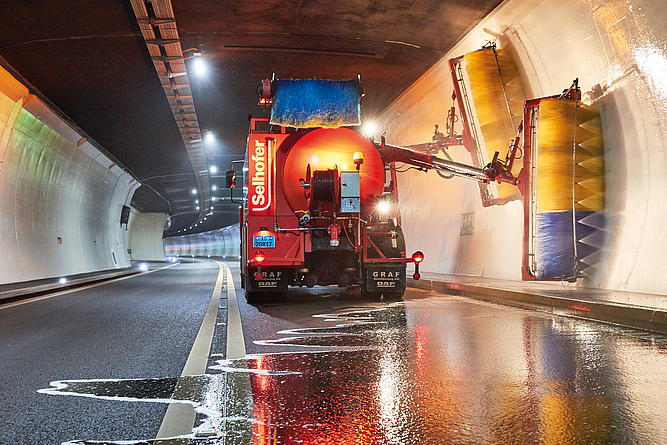
Tunnelwandbegleitung
Problem Korrosion
Korrosion ist laut DIN EN ISO 8044 „die Reaktion eines metallischen Werkstoffs mit seiner Umgebung, die eine messbare Veränderung des Werkstoffs bewirkt (Korrosionserscheinung) und zur Beeinträchtigung der Funktion eines Bauteiles oder eines ganzen Systems führen kann.“
Besonders in Straßentunneln, aber auch in vielen Bahntunneln, herrscht teil- bzw. zeitweise eine hochkorrosive Atmosphäre vor. Eingetragene Feuchtigkeit von Fahrzeugen, Kondensation und Undichtigkeiten im Tunnel sorgen zusammen mit Bremsabrieb, Abgasen und Tausalzen für eine unvorhersehbare Mischung korrosiver Elemente. Diese belasten alle Einbauteile im Tunnel und führen, je nach Zusammensetzung und Einwirkdauer auf den Oberflächen im Tunnel, zu unterschiedlich starker Korrosion.
In Bahntunneln, z. B. auf unterirdischen Bahnhöfen, ist auch die Flüssigkeit, die Menschen ausscheiden, nicht unerheblich. So beträgt der Flüssigkeitsverlust über die Haut 500 ml pro 24 h, der beim Ausatmen etwa 400 ml pro 24 h. Darin ist nicht die Flüssigkeit eingeschlossen, die aus Leckagen kommt oder von Fahrzeugen eingetragen wird. Geht man z. B. von 320 Personen, die sich im Jahrdurchschnitt auf einem unterirdischen Berliner S-Bahnhof aufhalten, aus, wären das 300 l pro h, die an Flüssigkeit abgegeben werden.
Um der Korrosion entgegenzuwirken, ist deshalb bei Einbauten wie Wandbekleidungen auf Korrosionsbeständigkeit zu achten. Korrosionsbeständigkeit definiert die Eigenschaft eines Metalls, äußeren Einflüssen zu widerstehen und in Verbindung mit anderen Elementen inert zu bleiben.
Die Korrosionsbeständigkeit ist primär abhängig von den Legierungselementen, aber auch die Oberflächen- und Gefügestruktur haben beträchtliche Bedeutung für die Beständigkeit eines Metalls gegenüber äußeren Einflüssen. Sie wird über den Korrosionsbeständigkeitsfaktor angegeben.
Der Korrosionsbeständigkeitsfaktor (engl. CRF) ergibt sich aus den Expositionsrisiken gegenüber Chloriden aus Salzwasser oder Streusalz (F1), gegenüber Schwefeldioxid (F2) und aus der Exposition gegenüber Abwaschen durch Regen sowie aus dem Reinigungskonzept (F3). Der CRF wird folgendermaßen berechnet
CRF = F1 + F2 + F3
Die DIN EN 1993-1-4:2015-10/Eurocode 3 beschreibt, wie der Korrosionsbeständigkeitsfaktor die fünf Korrosionsbeständigkeitsklassen (engl. CRC) bestimmt.
Bei einem Korrosionsbeständigkeitsfaktor < – 20 ist die Korrosionsbeständigkeitsklasse V gefordert.
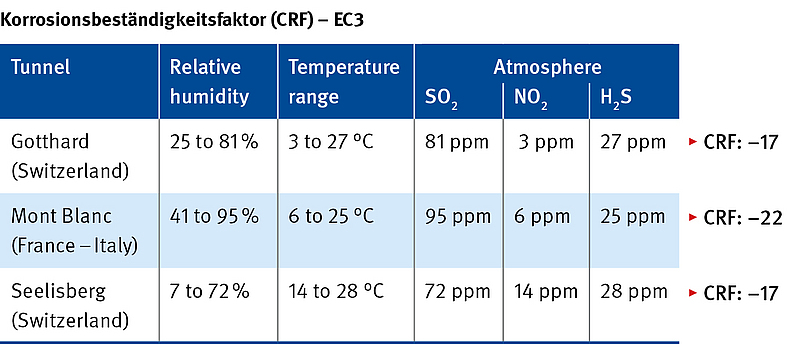
Korrosionsschutzanforderungen für Straßentunnel in Europa
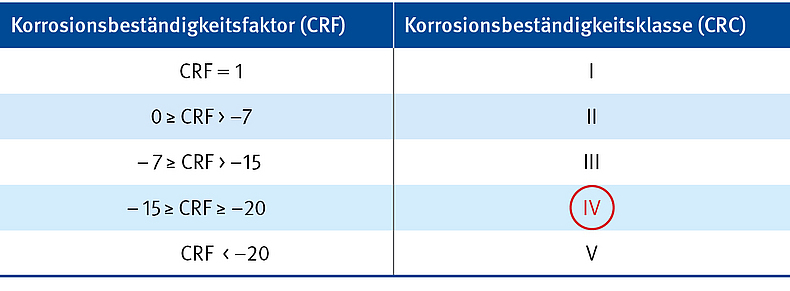
Korrosionsschutzanforderungen für Straßentunnel in Europa
Korrosionsschutzanforderungen für Straßentunnel in Europa
Für den Gotthard- und Seelisbergtunnel in der Schweiz sowie den Mont-Blanc-Tunnel in Frankreich/Italien wurde beispielhaft der Korrosionsbeständigkeitsfaktor ermittelt, der wiederum Auswirkungen auf die zu wählende Korrosionsbeständigkeitsklasse hat.
Aus den aktuellen Richtlinien ergibt sich die Anforderung an die Korrosionsbeständigkeit – Klasse IV für den Gotthard- und den Seelisberg-Tunnel, die vorliegenden Daten zum Mont-Blanc-Tunnel erfordern die Klasse V.
In Abhängigkeit von der geplanten Nutzungsdauer können auch Materialien aus abweichenden Korrosionsbeständigkeitsklassen gewählt werden. Die Verantwortung hierfür liegt in der Regel beim Bauherrn.
Dynamische Belastungen
Durch Tunnel fahrende Züge und Lkw belasten Einbauten mit regelmäßig wechselnden Lasten – was sich vor allem in Winddruck und -sog zeigt. Besonders Einzelzüge im Einbahnverkehr führen zu hohen resultierenden Kräften auf großflächige Einbauten, die ggfs. punktuell über geeignete Befestigungen abzutragen sind. Der hohe Nutzungsgrad stark frequentierter Verkehrsachsen führt hierbei zu dynamischen Belastungen aller Bauteile. Bei entsprechend niedrigerer Bemessungsgeschwindigkeit und/oder größerem Lichtraum im Tunnelquerschnitt fallen diese Druckspitzen entsprechend niedriger aus.
Neben den Lasten selbst spielt aber auch die Anzahl der Lastwechsel eine wesentliche Rolle. Unter Lastwechselreaktion versteht man die Änderung der Kraftrichtung (Wechsellast) oder der Intensität (Schwelllast) auf Einbauten. Diese ständig wiederkehrenden periodischen Einwirkungen können zum Ermüdungsversagen der Einbauten führen.
Die Unternehmensgruppe fischer hat bei einer angenommenen Nutzungsdauer von 50 Jahren die Lastwechsel für unterschiedliche Lastfrequenzen berechnet. Bei einer Lastfrequenz von drei Minuten finden 480 Lastwechsel pro Tag statt, was in 50 Jahren 8.760.000 Lastwechsel ergibt. Bei einer Lastfrequenz von einer Minute erhöht sich die Zahl der täglichen Lastwechsel auf 1.440. Hochgerechnet auf 50 Jahre wären das schon 26.280.000 Lastwechsel.
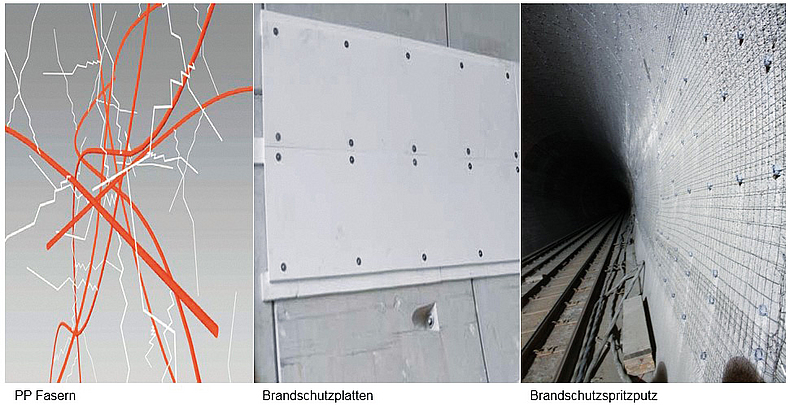
Brandschutz Tunnel
Brandschutzanforderungen
Nicht nur Korrosion und dynamische Belastungen spielen in Tunneln eine Rolle, sondern auch die Gefahr von Bränden und damit verbundene Brandschutzmaßnahmen. Ein Brand innerhalb eines Tunnels stellt enorme Anforderungen an die verbauten Materialien. Die Brandlast kann durch die nutzenden Verkehrsmittel sehr hoch sein. Durch die räumliche Enge können sehr hohe Temperaturen entstehen.
Um die Struktur des Bauwerks zu schützen und langfristige Nutzungsausfälle mit einem hohen volkswirtschaftlichen Schaden zu minimieren, werden besondere Betonrezepturen verwendet, PP-Fasern in den Beton gemischt, Brandschutzputze aufgetragen oder Brandschutzplatten auf der Oberfläche montiert. Neben Beschichtungen auf Beton oder Brandschutzplatten finden hier auch Paneele Anwendung, die besondere Oberflächeneigenschaften, wie hoher Reflexionsgrad, nachleuchtende Eigenschaften, Graffitischutz, oder architektonische Anforderungen erfüllen.
All diese Maßnahmen finden beim sogenannten Spalling (Abplatzen von Betonlagen an der Oberfläche durch Dampfdruck im Beton) Anwendung. Gleichzeitig soll sichergestellt werden, dass die Temperatur in der Bewehrungslagenebene begrenzt wird, um ein temperaturbedingtes Versagen der tragenden Strukturen auszuschließen.
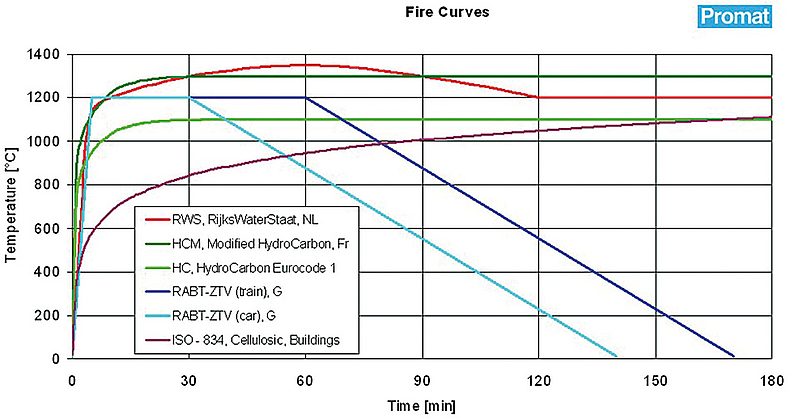
Brandkurven Tunnel
Ästhetische und weitere funktionale Ansprüche
Zunehmend kommen zu den Anforderungen an den Korrosions-, Belastungs-, Brand- und Schallschutz auch optische und dekorative Anforderungen. So wird bei Bedarf die architektonische Gestaltung mit hohen Reflexionsgraden und Fluchtrichtungsangaben kombiniert.
Eine Kombination der angesprochenen Anforderungen, zusammen mit dem Wunsch vieler Betreiber, die Bekleidungen zu Revisionszwecken oder nach Beschädigungen mit minimalen Betriebsunterbrechungen und ohne Spezialgeräte zu demontieren und neu zu montieren, stellt eine weitere Herausforderung dar. Die Kombination der Anforderungen führt zu neuen Produkten oder Produktkombinationen.
Der Markt hat darauf reagiert. Mittlerweile sind verschiedene Lösungen verfügbar, sowohl mit als auch ohne Durchdringung der Paneele bzw. Bekleidungsplatten.
Fazit
Die Ausführungen zeigen sehr deutlich die große Bandbreite der Anforderungen an Verkleidungen im Tunnel. Die Kombination ästhetischer und funktionaler Anforderungen erfordert neue, innovative und zugleich langfristig wirtschaftliche Lösungen von der Oberfläche über die Schutzfunktion bis zur dauerhaften Verankerung.
Autor
Ausgabe
BauPortal 3|2020