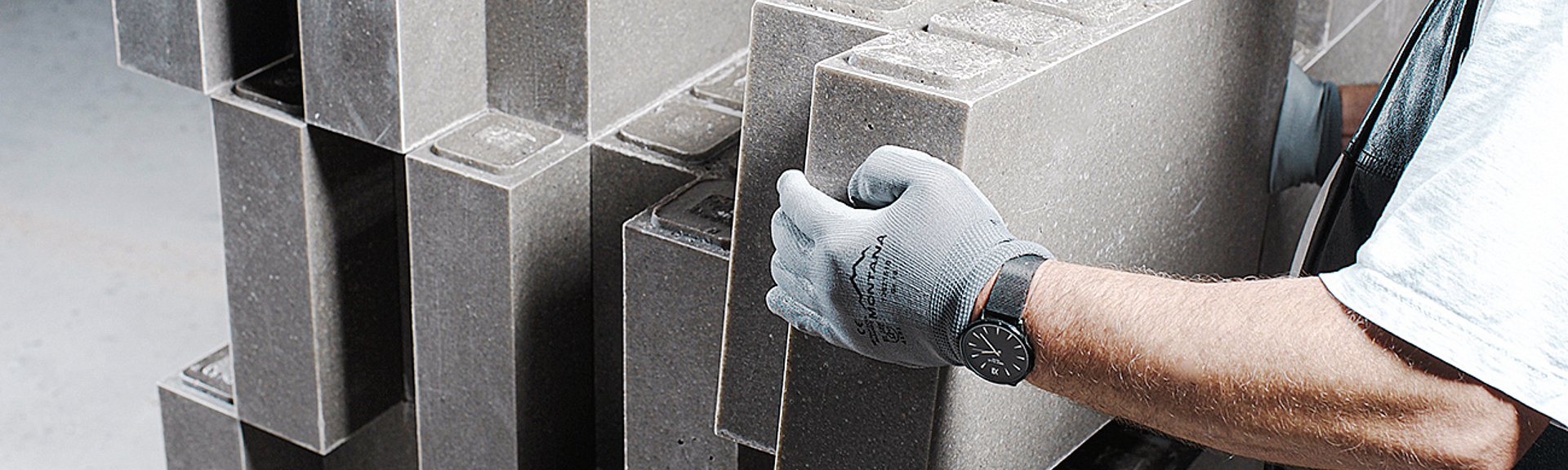
Zukunft des Bauens
Start-up-Lösungen für die Baubranche
Aus einer Kombination aus rieselfähigen mineralischen Stoffen und Polyester-Kunstharz stellt das Thüringer Unternehmen „Polycare“ Steinquader her, sogenannte „Polyblocks“. Diese können nach dem Lego-Prinzip leicht und flexibel in Handarbeit verbaut werden.
Seit mehr als zehn Jahren arbeitet Firmengründer Gerhard Dust daran, das neue Material und die notwendige Technologie nun weltweit zum Einsatz zu bringen.
Baustoff Polymerbeton
„Polyblocks“ können beispielsweise aus Wüstensand bestehen, der für die Herstellung von Baumaterial bisher eigentlich als unbrauchbar galt: Seine Körner sind zu glatt und rund. Die „Polycare“-Ingenieure binden diesen Sand nun mit Kunstharz, das derzeit zu einem Drittel aus recycelten PET-Flaschen entsteht. Dieser Anteil wird weiter erhöht, Expertinnen und Experten forschen bereits an einer rein biologischen Zusammensetzung des Polymerbetons und an biologischen Bindemitteln für die Bauindustrie.
Was macht die Lösung nachhaltig?
Der Baustoff dünstet, einmal ausgehärtet, laut „Polycare“ nicht aus. Polymerbeton ist schon nach zwanzig Minuten druck- und biegefest, absolut wasserdicht und frostbeständig. Er dämmt gut und hält deutlich länger als Beton. Wasser oder Mörtel wird für den Baustoff nicht benötigt. Auch der CO2-Ausstoß ist nach Unternehmensangaben 60 % niedriger als bei Zement, dessen Produktion 5 % der weltweiten CO2-Emissionen verursacht. Bei der Herstellung von Polymerbeton wird kaum Energie verbraucht. Das Volumenverhältnis Betonhülle/Isolierung liegt bei 1:4. „Polyblocks“ sind wiederverwendbar und vermeiden Bauschutt.
Wie wird gebaut?
Zwei Personen können in zwei Tagen ein knapp 60 qm großes Haus errichten: Stein für Stein wird für die Hausmauern an- und aufeinandergestapelt. Die Lego-ähnlichen Quader haben Noppen und bilden schnell eine Wand. Sie werden nicht geklebt, sondern verschraubt. Oberer Abschluss der Mauer ist ein stabilisierendes Gitter; Stahlstäbe werden von oben nach unten durch die Steine herabgelassen.
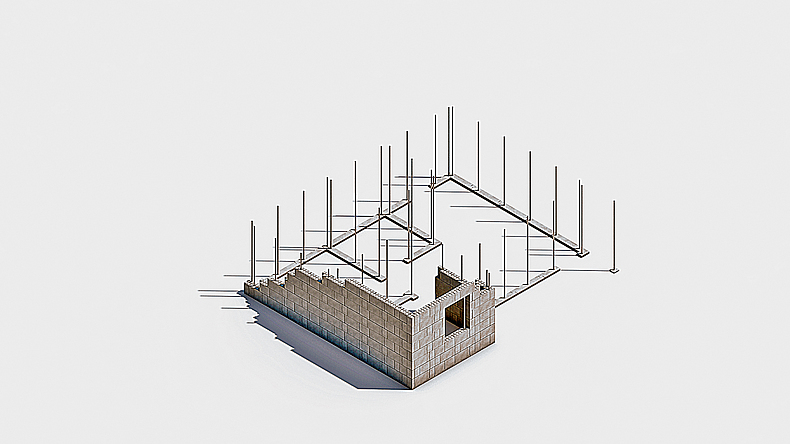
Stahlstäbe verleihen Hauswänden, die aus „Polyblocks" entstehen, Stabilität.
Die Konstruktionsweise der Häuser, mithilfe der Bauhaus-Universität Weimar entwickelt, sieht eine standardisierte sanitäre Inneneinrichtung vor und wahlweise speziellen Putz.
Beispiel Namibia
Den Start für eine weltweite Verbreitung der „Polyblocks“ bildet seit Februar 2019 die erste Fabrikation in Namibia. Schon vor zwei Jahren hatte die Hauptstadt Windhoek ein Wohnungsbauprojekt begonnen, zunächst mit 25.000 Häusern: Die ca. 16.000 bis 22.000 USD teuren Eigenheime sollen bezahlbaren Wohnraum für die Armen im Süden Afrikas bieten, so die namibische Regierung.
Ein erfolgversprechendes Modell?
„Polycare“ rechnet bei weltweiter Nachfrage mit einem Bedarf von 1,2 Milliarden Häusern. Die maschinelle Fertigung ließe sich z. B. auch in Katastrophengebieten installieren – für den schnellen Wiederaufbau zerstörten Wohnraums entweder direkt vor Ort oder indem die Fabrik künftig in einem Frachtcontainer Platz findet. Zudem werden lokale Fabrikationen eigenständige Unternehmen: „Polycare“ erhält nur in Form von Lizenzgebühren eine kleine Entschädigung.
Auch in Deutschland könnte dieses Modell aufgrund der überschaubaren Hauskosten erfolgversprechend sein. Die Tests des Baustoffs wurden erfolgreich absolviert.
Allerdings steht die amtliche Zulassung – Voraussetzung für eine Marktfreigabe – noch aus.
Polycare Research Technology GmbH & Co. KG
Autor
Ausgabe
BauPortal 2|2021
Das könnte Sie auch interessieren
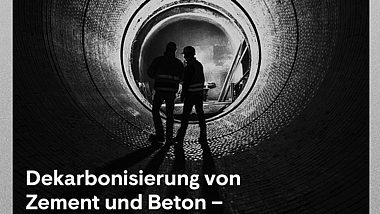
Studie zur Dekarbonisierung von Zement und Beton
Die deutsche Zementindustrie auf dem Weg in eine CO₂-freie Zukunft.
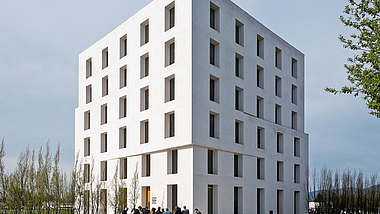
Nachhaltiges Bauen mit mineralischen Baustoffen
Beispielprojekte und Baustoff-Innovationen aus dem Massivbau-Netzwerk.
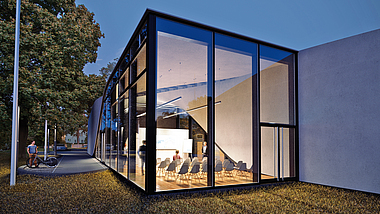