Tunnelbautechnik
Der Tunnel Feuerbach und seine baulichen Herausforderungen
Der Tunnel Feuerbach als Teil des Großprojekts Stuttgart 21 durchquert geologische Bereiche sowohl mit ausgelaugtem als auch mit unausgelaugtem, anhydritführendem Gipskeuper. Da Anhydrit bei Zutritt von Wasser in Gips umgewandelt wird, kann das Volumen um bis zu 60 % zunehmen. Um die Zuführung von Wasser zu verhindern, mussten umfangreiche technische und baubetriebliche Herausforderungen gemeistert werden.
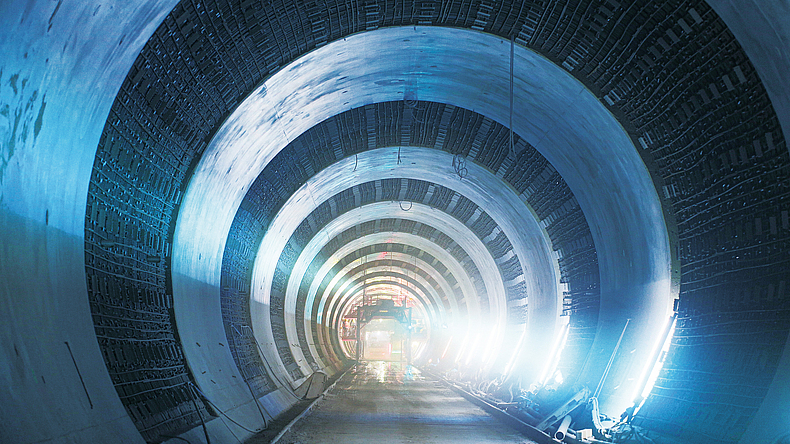
Im Rahmen des Großprojekts Stuttgart 21 wird der Tunnel Feuerbach als Baulos 2 im Planfeststellungsabschnitt PFA 1.5 errichtet. Dies umfasst die Herstellung des Tunnels Feuerbach, bestehend aus zwei parallelen Tunnelröhren, und den Umbau des Haltepunkts Feuerbach unter rollendem Rad. Der Tunnel Feuerbach erstreckt sich vom Haltepunkt Feuerbach im Norden bis zum Anschlussbereich an den Hauptbahnhof Stuttgart im Süden, wo sich die Röhren mit denen des Nachbarloses PFA 1.5 Los 3, Bad Cannstatt, in einem Verzweigungsbauwerk treffen (Abb. 2).
Die beiden Röhren haben eine Länge von je ca. 3 km und sind ca. alle 500 m mit Querschlägen verbunden. Die Andienung des bergmännischen Tunnels erfolgt lediglich über den Zwischenangriff Prag, einen 319 m langen Stollen. Dieser wird im späteren Betriebszustand als Fluchtweg und Entrauchungsstollen genutzt.
Die DB Projekt Stuttgart-Ulm GmbH erteilte im April 2012 den Auftrag zur Bauausführung an die Arge Tunnel Feuerbach, bestehend aus den Firmen Baresel Tunnelbau, Alfred Kunz Untertagebau und Bertschinger Bau.
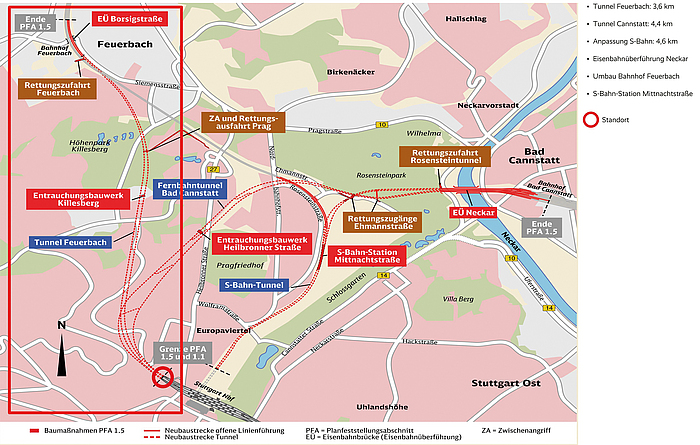
PFA 1.5, Übersicht, Los 2, Tunnel Feuerbach (rot umrandet)
Trockener Vortrieb mit Staubabsaugung
Der bergmännische Vortrieb führt durch stark wechselnde Baugrundverhältnisse, insbesondere durchfährt er ausgelaugten und unausgelaugten Gipskeuper. Das unausgelaugte Gestein ist bereichsweise anhydritführend, das Anhydrit (Calciumsulfat CaSO₄) ist in Lagen oder fein verteilt eingelagert. Im ausgelaugten Gipskeuper sind die Sulfatanteile durch zugeführtes Wasser bereits gelöst bzw. zu Gips (CaSO₄ · 2H₂O) umgewandelt, das Tongestein ist weitgehend entfestigt. Die Übergangszone zwischen beiden Bereichen ist wasserführend und wird Auslaugungsfront genannt. Der Tunnel Feuerbach durchfährt drei Bereiche mit Anhydritvorkommen, im Zuge der Vortriebsarbeiten wurden je Röhre fünf Auslaugungsfronten durchfahren (Abb. 3).
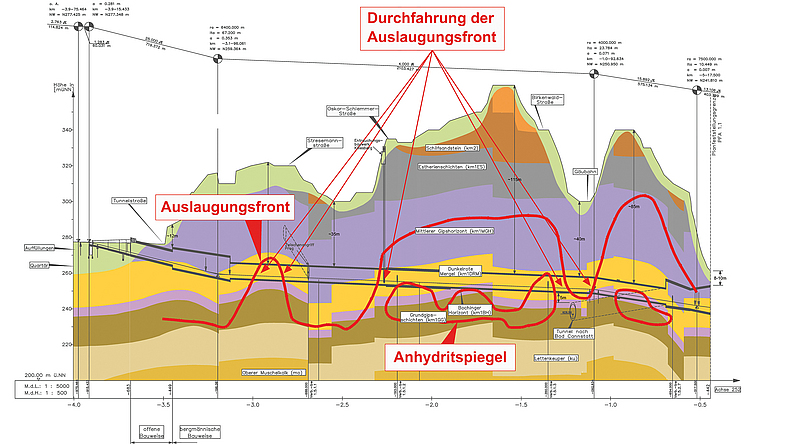
Beim konventionellen bergmännischen Vortrieb entsteht bei vielerlei Vorgängen durch die mechanische Bearbeitung des Gebirges Staub, so unter anderem bei Bohrarbeiten für Spreng- und Ankerlöcher, beim Lösen des Gebirges mittels Bagger, Fräse oder Sprengen und beim Schuttern. Der Umfang der Staubentstehung hängt von der Eigenfeuchte des Gebirges und der eingesetzten Gerätetechnik ab. Entstehender Staub wird in der Regel durch Bedüsung oder Benetzung mit Wasser eingedämmt.
Beim Tunnel Feuerbach wurden ca. 3.500 m in den Bereichen des unausgelaugten Gipskeupers aufgefahren, das Gebirge ist dort vollkommen trocken. Diese Abschnitte wurden als „trockener Vortrieb“ ausgeführt, also ohne dass Wasser dem Gebirge mit Quellpotenzial zugeführt werden durfte. Die Staubentwicklung musste mit umfangreichen Maßnahmen eingedämmt werden, um die gesetzlichen und normativen Anforderungen zu erfüllen.
Zunächst wurden die Bohrwägen mit Absaugeinheiten ausgerüstet, die den Staub direkt am Bohrlochmund fassen und einer Entstaubungs- bzw. Filteranlage zuführen (siehe Abb. 1). Weiter wurden kurz hinter der Ortsbrust Streckenentstauber mit einem Luftdurchsatz von 800 bis 1.500 m³/min. installiert, die einen großen Teil der rückströmenden Luft filterten.
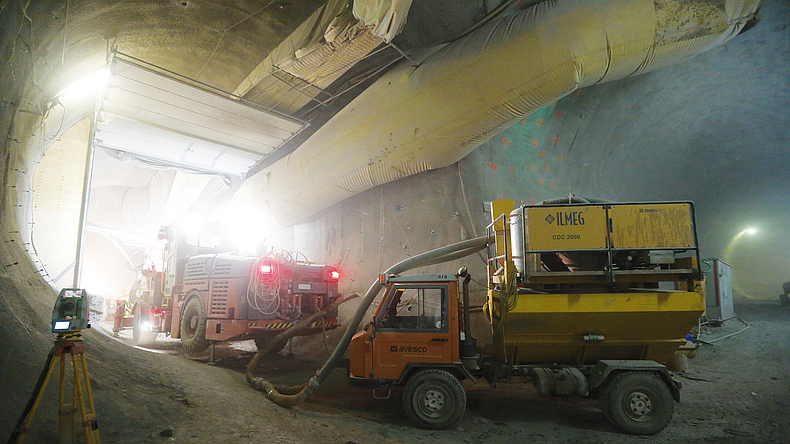
Um den nötigen Verbund zwischen den einzelnen Spritzbetonlagen herzustellen, wird in der Regel mittels Druckluft gründlich vorgereinigt bzw. auch vorgenässt. In den Bereichen des trockenen Vortriebs war dies nicht möglich, da ohne Wasserzugabe zu viel Staub in die Atemluft gelangt wäre. Daher setzte die ARGE im Sohlbereich Industriesauger mit einem Luftdurchsatz von 1.300 m³/h ein, um den Staub vor dem Auftragen weiterer Spritzbetonlagen zu fassen und zu beseitigen. Im Bereich der Strossenlaibung und der Firste verwendete die ARGE eine Bürste mit Absaugvorrichtung, die an einen Baggerarm montiert werden kann.
Um die Staubentstehung durch Schutterverkehr zu reduzieren, wurden auf der Fahrbahn Calciumchloridflocken aufgebracht. Diese reagieren mit der Luftfeuchtigkeit und bilden dadurch eine leicht feuchte Fahrbahnoberfläche. [1]
Erkundungsbohrungen und vorauseilende Injektionen
Während des Tunnelvortriebs wurde die Lage des anhydritführenden Gesteins intensiv erkundet. Hierzu wurden in einem Abstand von 20 m Kernbohrungen mit einer Länge von i. d. R. 15 m in Sohle und Firste gebohrt. Auf diese Weise wurden die anstehende Geologie sowie der Anhydritgehalt mittels insgesamt ca. 4.300 m Bohrkernen bestimmt. Ebenso wurden an der Ortsbrust regelmäßig Proben zur Anhydritbestimmung entnommen sowie vereinzelt vorauseilende Erkundungsbohrungen ausgeführt. In den Bereichen der Auslaugungsfront waren vortriebsunterbrechende vorauseilende Injektionen mit PU-Harz erforderlich, um Wasserzutritte in die aufzufahrenden Bereiche zu vermeiden. Nach jeweils sechs Vortriebsmetern wurden trichterförmige, 8 m lange Injektionsbohrungen hergestellt und anschließend injiziert. Daraufhin wurden die nächsten 6 m Tunnel aufgefahren. Dieser Vorgang wurde so oft wiederholt, bis die jeweilige Auslaugungsfront durchfahren war (Abb. 4).
Beide Tunnelröhren wurden vom Zwischenangriff Prag aus gleichzeitig jeweils in Richtung Feuerbach sowie in Richtung Hauptbahnhof aufgefahren, sodass durchgehend Angriffspunkte auf vier Vortriebsästen vorhanden waren. Durch die Fülle an vortriebsunterbrechenden Maßnahmen entschied sich die ARGE, nur mit drei Vortriebsmannschaften zu arbeiten, um einen kontinuierlichen Personaleinsatz zu gewährleisten.
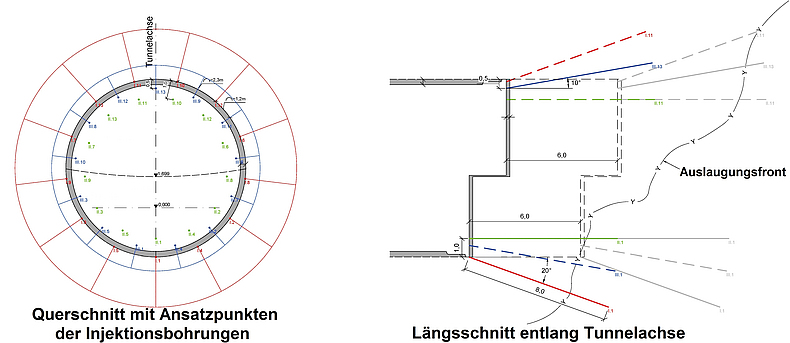
Systematische nachlaufende Injektionen mit Acrylatgel
Durch Ausbruch und Sicherung entsteht rings um den Tunnel eine Auflockerungszone, in der die Durchlässigkeit des Gebirges deutlich erhöht ist (Durchlässigkeitsbeiwert > 10–3 m/s). Um in den Tunnelabschnitten im anhydritführenden Gebirge die Durchlässigkeit der Auflockerungszone wieder zu reduzieren, wurden umfangreiche Abdichtungsinjektionen mit Acrylatgel ausgeführt. Hierzu wurden je nach Lage des anhydritführenden Gesteins sowie der wasserführenden Schichten 4–10 m lange radiale Injektionsbohrungen mittels eines programmierten Bohrschemas (Ansatzpunkt, Richtung, Bohrtiefe) abgeteuft. Die Injektionen erfolgten zunächst in einer a-Serie in Querschnitten alle acht Tunnelmeter, dann in einer b-Serie zwischen den Injektionspunkten der a-Serie in denselben Querschnitten, anschließend a- und b-Serie in dazwischenliegenden Querschnitten usw. bis zu einem Abstand der Querschnitte von einem Meter. Nach Injektionen aller a- und b-Serien wurde bei Bedarf die c-Serie (Bohrlöcher in einem Querschnitt zwischen den Bohrungen der a- und b-Serie liegend) injiziert (beispielhafter Injektionsquerschnitt siehe Abb. 5). So wurde nach und nach das Injektionsraster auf bis zu 1 × 1 m verdichtet. Die Injektionseinheiten sowie die Bohrwägen durchfuhren auf diese Weise ein und denselben Tunnelabschnitt bis zu zwölf Mal. Die jeweils geringere Aufnahme von Injektionsmaterial durch den Fels diente dabei als Kontrolle des Injektionserfolgs. [2]
Die Packerstellung für die Acrylatgelinjektionen befindet sich, je nach Spritzbetonschalenstärke, ca. 30 cm tief im Bohrloch im Fels liegend. Sämtliche Injektionsbohrungen wurden in einem zweiten Schritt mit separaten Injektionseinheiten mit niedrigviskosem PU-Material verschlossen. Hier befindet sich die Packerstellung im Spritzbeton. Auf diese Weise wurde die Acrylatgelinjektion luftdicht versiegelt und ggf. vorhandene Wasserwegigkeiten zwischen Spritzbeton und Gebirge mit PU abgedichtet. Nachdem ein Abschnitt (i. d. R. 100 bis 200 Tunnelmeter) vollständig injiziert worden war, wurden abschließend Durchlässigkeitsversuche durchgeführt. Ziel war es, durch die Injektionen einen Durchlässigkeitsbeiwert von < 10–7 m/s zu erreichen. Wurde diese Durchlässigkeit nicht erreicht oder (geringfügige) Wasserzutritte in bereits injizierten Abschnitten festgestellt, musste dort lokal nachinjiziert werden.
Um Längsläufigkeiten des Wassers im Bereich der Auslaugungsfront in die Anhydritbereiche zu vermeiden, wurden Dammringe hergestellt. Diese bestehen aus einem 1 m starken und 5 m breiten Ring aus stahlfaserbewehrtem Spritzbeton. Zudem wurden Injektionen mittels Acrylatgel durch bis zu 11 m lange Injektionsbohrungen vorgenommen (Abb. 5).
Zur Qualitätssicherung und Dokumentation wurden zahlreiche Parameter während der Injektion mit hoher Genauigkeit erfasst, u. a. die Durchflussraten der einzelnen Acrylatgelkomponenten sowie des Gemischs hinter dem Mischkopf, der Injektionsdruck in der Verpressstrecke und die Injektionsdauer. Eine Überschreitung der festgelegten Toleranzen wurde dem Pumpenfahrer automatisch gemeldet. Die Injektionsdaten von täglich bis zu 500 Injektionen wurden mit einem digitalen Daten- und Dokumentationsmanagementsystem erfasst, verwaltet und ausgewertet.
Insgesamt wurden im Tunnel Feuerbach ca. 310 km Bohrungen für Acrylat- und PU-Injektionen mit zwei Bohrwägen hergestellt und ca. 2,5 Mio. Liter Injektionsmaterial mit drei Injektionseinheiten für Acrylatgel sowie zwei Injektionseinheiten für PU verpresst, insgesamt mit bis zu zwölf Pumpen. Die Injektionen erfolgten dem Vortrieb nachlaufend vor Einbau der Innenschale.
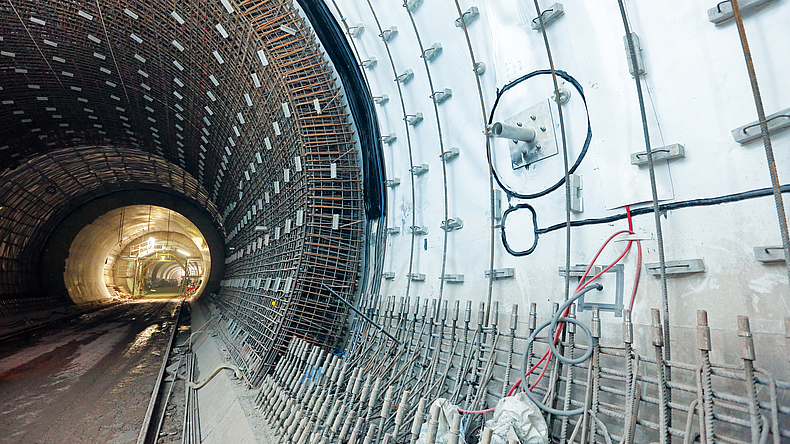
Hochbewehrte Innenschale
Im Gebirge, das durch den Tunnel Feuerbach durchfahren wird, liegt der Anhydritspiegel des unausgelaugten Gipskeupers i. d. R. im unteren Bereich des Tunnelquerschnittes, in Höhe der Tunnelsohle. Dringt nun Wasser aus darüberliegenden Schichten (z. B. Bochinger Horizont, Auslaugungsfront) in das anhydritführende Gebirge ein, so können dort Quelldrücke entstehen, die zunächst seitlich auf die Innenschale einwirken [3]. Bei der Bemessung der Innenschale führt dies dazu, dass die stärksten tangentialen Zugspannungen in der Stahlbetonschale insbesondere im Bereich der Ulmen an der Luftseite sowie in der Sohle an der Bergseite aufgenommen werden müssen. Dazwischen sowie im Übergang zur Firste wird eine massive Schubbewehrung erforderlich. Ein durchschnittlicher hochbewehrter Block hat damit an der Innenseite drei radiale Lagen Stabstahl Durchmesser 25 mm alle 15 cm im Bereich der Ulmen sowie Schubbügel und Schubdübel alle 15 cm.
Von insgesamt ca. 500 bergmännisch herzustellenden Tunnelblöcken liegen 218 Stück in anhydritführendem Gebirge und werden auf die oben beschriebene Weise hochbewehrt. Die Regelblocklänge beträgt 12 m, der Bewehrungsgrad beträgt im Durchschnitt ca. 220 kg/m³, im höchstbewehrten Block sogar 476 kg/m³ (bei einer Innenschalendicke von 70 cm). Für einen hochbewehrten Regelblock müssen somit ca. 80 t Betonstahl verlegt werden, davon ca. 13 t Schubbewehrung und bis zu 2.200 Schubdübel.
Aufgrund der großen erforderlichen Übergreifungslänge wären bei einem klassischen Übergreifungsstoß Bewehrungsarbeiten hinter der luftseitigen aufgehenden Anschlussbewehrung der Sohle wegen der dichten Bewehrungsführung nicht möglich. Daher wird der Bewehrungsanschluss zwischen Sohl- und Gewölbebewehrung mittels Positions-Muffen ausgeführt. Insgesamt werden so ca. 120.000 Schraubmuffen eingebaut (siehe Abb. 6).
Der Bewehrungseinbau erfordert insbesondere im Gewölbe ein sehr hohes Maß an Lagegenauigkeit, da über das Stellen des Schalwagens nahezu keine Korrekturen vorgenommen werden können. Ebenso müssen Verformungen, die durch die hohe Masse des Bewehrungskorbs (im Mittel 55 t im Gewölbe) entstehen, vermieden werden. Daher wurden schwere Gitterträger mit geschraubten Flanschen statt herkömmlicher Tragbögen verwendet. Diese wurden zunächst lagegenau eingemessen und aufgebaut, die äußere Bewehrung musste anschließend dahinter eingefädelt werden. Seit Juni 2019 ist die ARGE auf ein Spannringsystem umgestiegen. Hier werden für die Gewölbebewehrung ca. alle 60 cm vorgebogene Stahlstäbe mit Durchmesser 20 mm als Ring lagegenau mittels Abstandhalter gegen die Tunnellaibung vorgespannt (siehe Abb. 6). Dieser Ring bildet den äußeren Radius des Bewehrungskorbs. Die Bewehrung kann nun komplett von außen nach innen aufgebaut werden. Der Verlege- sowie der Vermessungsaufwand bei den Gewölbeblöcken konnten durch diese Maßnahme reduziert werden.
Die Bewehrungsarbeiten werden im Durchlaufbetrieb Tag und Nacht ausgeführt. Nach der Einarbeitungsphase konnte schließlich die Gewölbebewehrung in vier bis fünf Schichten hergestellt werden. Die Herstellung der hochbewehrten Gewölbe im Tagestakt ist nicht möglich, da alleine die Betonierzeit eines metrigen Gewölbes (235 m³ ohne Überprofil) bis zu 16 Stunden dauert. Von vornherein wurde auf die Planung eines Lückenschlusses verzichtet, diesen zu bewehren, hätte bereits ca. zwölf Stunden erfordert. Stattdessen entschied sich die ARGE, die Gewölbe auf Lücke mit Vorläufer- und Nachläuferblöcken herzustellen. Die Lückenblöcke werden über einen nachlaufenden, zweiten Bewehrungswagen bereits während der Herstellung der Vorläuferblöcke bewehrt.
Für die hochbewehrten Blöcke wird ein Beton C45/55 mit der Konsistenzklasse F6 (sehr fließfähig) eingesetzt. Die speziell für das Projekt entwickelte Zementsorte verhindert eine zu große Hydratationswärme. Die Betonrezeptur wurde in etlichen Versuchen entwickelt und in zwei Probeblöcken auf der Baustelle getestet.
Eine weitere Besonderheit bei der Herstellung der Innenschale ist der bergseitige Einbau von Bentonitmatten hinter der KDB-Abdichtung. Diese sollen die Längsläufigkeiten von Wasser entlang der Spritzbetonschale vermeiden, da sich das Bentonit bei Kontakt mit Feuchtigkeit unter leichtem Quellen verschließt und Wasserwegigkeiten somit reduziert. Der Einbau und die Funktionalität der Bentonitmatte wurden im Vorfeld über einen Großversuch getestet. Alle Bereiche mit Bentonitmatten werden nach der Betonage nach Abklingen des Schwindvorgangs mit Zement hinterlegt, sodass der Ringspalt verfüllt wird und die Bentonitmatte kraftschlüssig zwischen Abdichtung und Spritzbetonaußenschale angepresst wird. Dadurch wird das Auswaschen des Bentonits in einen ggf. vorhandenen Hohlraum verhindert und die abdichtende Wirkung gewährleistet.
Des Weiteren werden temporäre Edelstahldrainagen (siehe Abb. 6) eingebaut. Diese sollen Wasserzutritte in das anhydritführende Gebirge in den ersten Jahren nach der Herstellung der Innenschale verringern, dadurch eine Selbstabdichtung des Gebirges ermöglichen (Auskristallation von Gips in Trennflächen und Klüften, Schließen von Wasserwegigkeiten) und den Aufbau des Quelldrucks verlangsamen. [3]
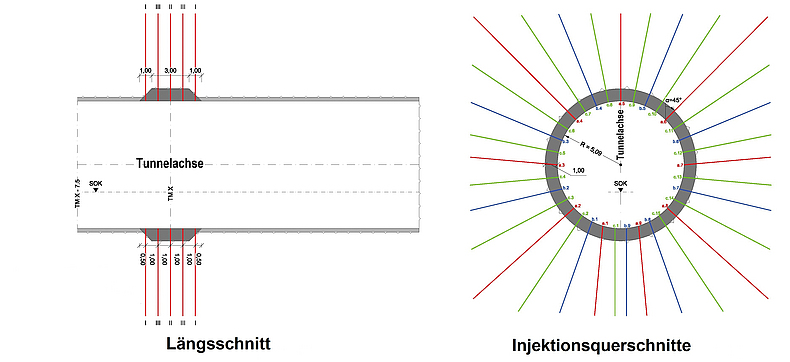
Fazit
Bei der Herstellung des Tunnels Feuerbach in der sensiblen Geologie des anhydritführenden Gipskeupers kam eine Reihe besonderer Maßnahmen zum Einsatz. Bereits während der Vortriebsarbeiten musste jegliches Einbringen von Wasser in anhydritführendes Gebirge vermieden werden. Die daraus resultierende Staubentwicklung im trockenen Vortrieb konnte durch eine Reihe technischer Maßnahmen, wie Absaugung oder Abbinden des Staubs, reduziert werden. Des Weiteren mussten Wasserwegigkeiten in geologischen Übergangsbereichen sowie in durch den Vortrieb entstandenen Auflockerungszonen mittels umfangreicher systematischer Injektionen abgedichtet werden. Aufgrund der immensen Quelldrücke wurde in weiten Teilen des Tunnels eine 100 cm starke hochbewehrte Innenschale eingebaut. Da in der Hauptbauphase gleichzeitig Vortriebs- und Profilierungsarbeiten ausgeführt, mit bis zu fünf Einheiten und zwei Bohrwägen injiziert sowie die Innenschale mit zwei Schalzügen hergestellt wurden, bestand eine weitere Herausforderung in der Koordination der Gewerke und der Aufrechthaltung der Baustellenlogistik. Alle Herausforderungen konnten dank der hohen Fachkompetenz der Beteiligten und der vertrauensvollen Zusammenarbeit der Projektpartner erfolgreich gemeistert werden.
Literaturhinweise
- [1] Schmidberger, D.; Schimmelpfennig, M.: Staubminimierungskonzepte für trockene Vortriebe. Artikel im BauPortal 3/2019
- [2] Lienhart, C.; Schmitt, D.; Wittke, M.; Wittke, W.: Planung und Ausführung von Injektionen im anhydritführenden Gipskeuper. Vortrag anlässlich des 4. Felsmechanik- und Tunnelbau-Tags im WBI-Center Weinheim 2018
- [3] Wittke, W.; Wittke-Gattermann, P.; Boettcher, A.: Bemessung und Bewehrung der Stahlbetoninnenschale im anhydritführenden Gebirge. Vortrag anlässlich des 4. Felsmechanik- und Tunnelbau-Tags im WBI-Center Weinheim 2018
Autor
Ausgabe
BauPortal 2|2020